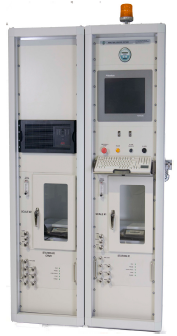
The APS carbon canister testing system (C2K) complies with and follows the US Environmental Protection Agency CFR 40,86.132 and California Air Resources Board evaporative emission standards and testing procedures.
In order to support certification compliance testing, research, and development, C2K adopts a unique driver approach and user configurable testing program, powerful data collection system, and flexible report generation method. The modular platform design concept ensures that 9 independent channels can be tested simultaneously.
Our advantages
APS has 50 years of experience in manufacturing carbon canister testing systems;
APS can control up to 9 independent channel charcoal canister tests simultaneously;
The APS software control system has powerful functions, and users can customize multiple testing processes;
The desorption air of APS is controlled by a mass flow controller, which fully complies with regulatory requirements;
The production of APS is completely in accordance with China's strict explosion-proof level ZONE 0;
APS safety system: It has over limit protection and constantly monitors whether HC leaks. After reaching the limit value, the software will automatically stop. If there is no automatic stop, there is also a manual emergency stop button, providing dual safety protection;
Modular design: The solenoid valve and mass flow controller are assembled in different areas to avoid electric sparks caused by the on-off of the solenoid valve;
Unique nitrogen bubble fuel vapor generator;
After sales service, EST itself is a manufacturer of carbon canister testing systems, including manufacturing, production, debugging, and after-sales service. The combination of APS and EST can better ensure the quality of after-sales service;
control system
The C2K control system is based on the Pentium processor PC, and the operating interface is based on the Windows system. APS software provides an intuitive graphical user interface that facilitates user operation of the system.
The CK control system includes the following user-defined settings:
Dynamic detachment: Users can configure the step sequence.
Carbon canister pressure drop measurement: can automatically set flow range: 10L/min, 20L/min, 30L/min, 40L/min, 50L/min, 60L/min, 70L/min, 80L/min.
Carbon canister sealing test: immersion leakage inspection, 14Kpa, 30s, pressure and time adjustable.
Carbon canister desorption: Air requirement: 77 ± 9F (25 ℃± 5 ℃), clean air, 300 times the bed volume for desorption of carbon canister.
Carbon canister pretreatment
Adsorption and desorption require at least 10 cycles to reach stability. When the auxiliary canister adsorbs to 2g and breaks down, the main canister is loaded.
Assist the carbon canister in adsorbing 2g and breaking down to determine the working capacity of the main carbon canister.
Users can choose a work ability testing program.
C2K provides the following setting options:
Desorption cycle setting
Detachment flow rate (SLPM - standard liters per minute)
Carbon canister volume value (1-9999)
Desorption auxiliary charcoal canister (y/n)
Pause time after detachment completion (minutes)
Loading (adsorption) cycle setting
Adsorption flow rate (g/hour)
Butane volume percentage (1% - x%)
Pause time after loading completion (minutes)
Use the range value of the main carbon canister (y/n)
Use auxiliary charcoal canister range value (y/n)
Other functions
Number of loading/desorption cycles (1-9999)
Use fuel vapor (y/n)
Fuel Vapor Flow Rate (SLPM)
Leakage monitoring (y/n)
Load initial monitoring (y/n)
Detachment completion monitoring (y/n)
Loading method
Not loaded (y/n)
Time loading (minutes)
Doubling work ability (x-x)
Quality loading (g)
Overflow loading (g)
Security and Monitoring System
Password protection
Gas monitoring
L Over limit alarm
Automatic shutdown
Emergency stop button
system requirements
220V 50Hz AC, single-phase;
20 SCPM (1m ³=35.315 cubic feet); 90psi is 620KPa (1psi=6.895kPa) clean and dry compressed air.
Flow and accuracy
Standard loading flow rate of 300g/hour;
40g/min gasoline vapor loading;
3600g/hour ORVR loading;
25SLPM desorption air;
Maximum weighing weight of the balance: 7kg; Balance resolution: 0.01g;
Accuracy: ± 1% of full scale;
Repeatability: ± 0.015% of full scale.
Nitrogen Bubble Fuel Steam Generator
Principle: Use nitrogen bubbles to pass through the fuel, generating a large amount of vortices and ultimately producing fuel vapor.